High cycle molding machine
- SANKO GOSEI
- Feb 8, 2023
- 1 min read
High-cycle molding requires the introduction of molding machines developed specifically for high-cycle molding, including injection, lightweighting, and mold opening and closing, as well as molds designed for high-cycle molding.
High-cycle molding also requires the introduction of molding machines developed exclusively for high-cycle molding.
Injection molding machines with the ability to perform continuous molding with a combination of injection mechanism and mold open/close mechanism that matches each product.
Injection molding with a combination of injection mechanism, mold open/close mechanism, etc. that match each product can realize the shortest cycle time possible.。
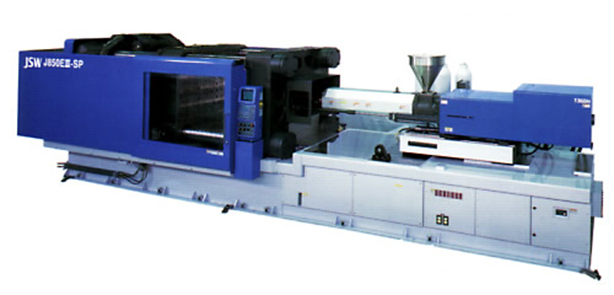
Requirements for high-cycle molding machines
1) High-speed injection
(2) High-speed mold opening/closing
(3) High-speed plasticizing capability
(4) Thermal measures
(5) Low noise
⑥Space saving
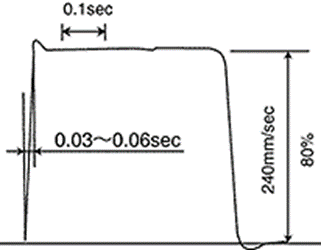
Injection speed response is important for thin-wall control with short injection times (0.5 sec. or less).
The SP machine improves speed response, minimizes overshoot and undershoot, improves filling performance, and caps overfilling.
SP machines improve the speed response, minimize overshoot and undershoot, improve filling performance, and reduce overfilling.
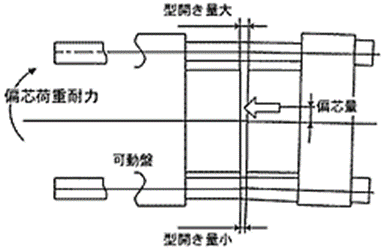
Minimization of moldboard deformation by increasing the rigidity of the moldboard, as well as the rigidity of the tie bar and toggle mechanism.
The reduction of assembly tolerances allows the moldboard to maintain the degree of shift even under loads at any angle.
This high eccentric load capacity allows for high speed mold opening/closing, cavity internal pressure variation, injection compression molding, etc.
This high eccentric load capacity enables high precision mold transfer even under high-speed mold opening/closing, cavity internal pressure variation, injection compression molding, and other conditions.
Comments